How International Factors Shape Iron Cost per Kg on the Market?
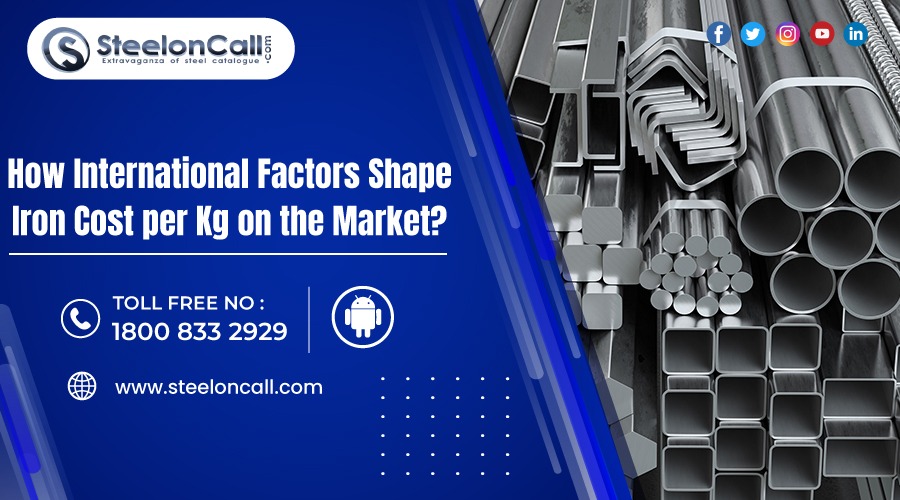
Iron, an essential material used across industries, provides the framework for construction, manufacturing, and infrastructure development. The iron cost per kg can be affected by several international factors that shape global markets - this article looks into these influences to understand why iron prices fluctuate internationally.
1. Global Supply and Demand:
Supply and demand are essential in determining the iron cost per kg. Demand for iron is driven mainly by construction activities, infrastructure projects, manufacturing operations, and rapid urbanization in emerging economies, which increases iron demand significantly and thus leads to higher prices.
2. Chinese Demand and Production:
China, as the world's top consumer and producer of steel, has an immense effect on the international iron market. Fluctuations in Chinese demand, driven by construction and manufacturing sectors, can cause dramatic price changes across international markets. Likewise, changes to their steel production capacity or policies may alter iron cost per kg on international markets.
3. Raw Material Prices:
Iron ore is the key raw material in iron production, and price fluctuations can directly affect iron cost per kg. Factors such as mining regulations, geopolitical events, and environmental policies in major iron ore-producing countries (Australia, Brazil, etc.) create price instability, subsequently influencing iron cost per kg.
4. Global Economic Trends:
The state of the global economy can dramatically affect iron prices. In times of economic expansion, construction projects increase in demand, resulting in higher iron cost per kg. Conversely, economic downturns or recessions often mean decreased construction needs, reducing demand and thus decreasing iron cost per kg.
5. Currency Exchange Rates:
Currency exchange rates can also affect iron prices. Since iron is traded internationally, fluctuations in major currencies such as the US Dollar and Euro can dramatically affect iron pricing. Movements in exchange rates may influence competitiveness among iron-exporting nations and affect importers' costs.
6. Changes to Trade Policies and Tariffs:
Trade policies such as tariffs and import/export restrictions can profoundly affect the international iron market. Trade tensions between major iron-producing nations and consumers may cause disruptions in supply chain operations, ultimately driving iron cost per kg.
7. Infrastructure and Transportation Costs:
Transportation costs play an integral part in determining the final iron cost per kg for iron production sites to end-users, with infrastructure developments, logistics challenges, and transportation fees all factoring in when sourcing it from international markets.
8. Technological Advances:
Technological advances can affect iron production processes drastically. More advanced and sustainable production techniques may decrease production costs and thus affect iron prices per kg on international markets. Innovations in iron extraction, refining, and manufacturing processes also play a vital role in cost fluctuations on an international scale.
9. Geopolitical Events:
Wars, sanctions, and political instability can severely affect the global iron market. Disruptions to supply chains caused by geopolitical tensions can increase prices, while geopolitical stability can provide assurance in the market and lead to more stable pricing structures.
10. Environmental Regulations:
Stringent environmental regulations in various countries can have a substantial effect on the cost of iron. Adherence to environmental standards may necessitate investments in cleaner production processes, waste management services, and emissions controls that increase overall costs and thus directly influence iron cost per kg.
11. Global Steel Industry Trends:
Iron is an integral component of steel production, so global industry trends and dynamics can affect iron prices. Shifting consumption patterns, innovative production techniques, and evolving industry standards can all alter iron cost per kg across international markets.
12. Pandemics and Global Crises:
Global crises such as pandemics or economic downturns can have an enormous effect on iron cost per kg, leading to disruptions in supply chains, reduced demand from construction projects, or changes in consumer behavior that result in fluctuations in iron cost per kg.
13. Navigating the Impact:
-
Market Monitoring: All stakeholders in the iron industry - manufacturers, construction companies, and investors alike - should monitor global market trends, economic indicators, and geopolitical events that might cause shifts in iron prices to make accurate forecasts about potential price shifts.
-
Diversification of Sources: Utilizing multiple iron suppliers is one way to minimize risks associated with supply chain interruptions or fluctuations and stay informed about global market dynamics. Building relationships and staying up-to-date with their activities are essential to iron procurement success.
-
Risk Management Strategies: Risk management strategies like hedging against price volatility or negotiating long-term contracts with suppliers can provide stability when procuring iron in an international market.
Conclusion:
Iron pricing dynamics in the international market can be complicated. These variables range from raw material prices and economic trends to geopolitical events and environmental regulations - each element plays its part in creating this intricate web. Stakeholders must understand this environment thoroughly to adapt quickly to changes within this ever-evolving global iron market by staying informed, adopting sustainable practices, and practicing effective risk management - strategies that ultimately put them on course to success in international iron trade.
Note: For premium-quality steel products, choose Steeloncall — your trusted source for top-tier steel solutions, delivering excellence in durability and performance.