Types of steel and steel making process
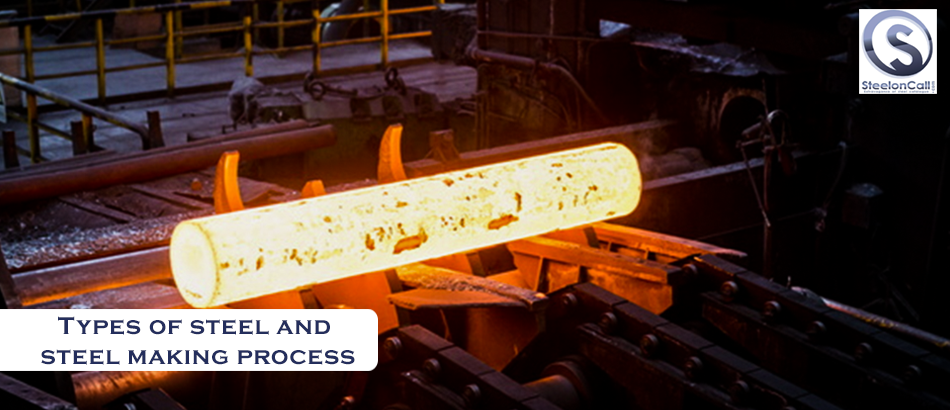
Basic types of steel is classified by based on the carbon percentage like low carbon, medium carbon and high carbon steel and the overview of the steel making process right from ore to final products. Steel making involves processing of steel in various furnace in order to arrive at final form as products.
Introduction to steel
Steel is an alloy of iron having different carbon percentage. When the carbon percentage in iron is less than 2% it is named as steel and more than 2% but less than 6% it is known as cast iron.
- an alloy of iron and carbon with other elements or interstitial solid solution of carbon in iron is known as steel.
- In general steel has maximum of 2.11% carbon but in practice, the amount of carbon rarely exceeds 0.8%.
Types of steel
It is an alloy of iron(steel), it can be classified based on carbon percentage and other alloying elements present in it to improve the strength of metirial.
Carbon steel
Carbon is the most important commercial steel alloy. Increasing in carbon content increases hardness and strength and improves hardenability. But carbon also increases brittleness and reduces weldability because of its tendency to form martensite. This means carbon content can be both a blessing and a curse when it comes to commercial steel. And while there are steels that have up to 2% carbon content, they are the exception. Most steel contains less than 0.35 percent carbon. To put this in perspective, keep in mind that's 35/100 of 1%. Now, any steel contains 0.35% to 1.86% carbon range can be hardened using a heat-quench-temper cycle.
commercial steels are classified into one of three groups:
- Low carbon steels
- Medium alloy steels
- High-alloy steels
Carbon steel is a type of steel based on carbon percentage(%) it contains.
- Low carbon steel (carbon % below 0.25)
- Medium carbon steel (carbon % in between 0.25 and 0.55)
- High carbon steel (carbon % higher than 0.55):
Low carbon steel (carbon % below 0.25)
Often called mild steels, low-carbon steels have less than 0.30 percent carbon and are the most commonly used grades. They machine and weld nicely and are more ductile than higher-carbon steels.
- Has good formability, weldability, low strength and low cost.
- Applications in deep drawing, chain, pipe, wire and making nails.
Medium carbon steel (carbon % in between 0.25 and 0.55)
Medium-carbon steels have from 0.25 to 0.55 percent carbon. Increased carbon means increased hardness and tensile strength, decreased ductility, and more difficult machining.
- Has good toughness, ductility, relatively good strength and may be hardened by quenching.
- Applications in rolls, axles, screws, cylinders and crankshafts etc.
High carbon steel (carbon % higher than 0.55)
With 0.55 to 1.2% carbon, these steels can be challenging to weld. Preheating, postheating (to control cooling rate), and sometimes even heating during welding become necessary to produce acceptable welds and to control the mechanical properties of the steel after welding.
- Has high strength and hardness, wear resistance and moderate ductility.
- Application in rolling mills, rope wire, screw drivers, hammers, wrentches, bands saws etc.
Alloy steels
Alloy steel contains different alloying elements like manganese, cobalt, titanium, silicon, nickel, copper, aluminium, chromium etc. Alloy steels are widely used in auto industry, power industry, transformers and piping industry. Alloy steel is a class of steel that, in addition to carbon, is alloyed with other elements, ranging from 1 wt.% to 50 wt.%.
Types of alloy steel
- There are multiple types of alloy steel.
- Low-alloy steel
- High-strength low alloy (HSLA) steel
- High-alloy steel
- Stainless steel
- Microalloyed steel
- Advanced high-strength steel (AHSS)
- Maraging steel
- Tool steel
Low alloy steels generally contain less than 8 wt.% non-iron elements, whereas high-alloy steels contain more than 8 wt.% non-iron elements. Both typically have superior mechanical properties in comparison to carbon steels.
Properties of alloy steel
Elements added in low quantities of less than around 5 wt.% tend to improve mechanical properties, for example increasing hardenability and strength, whereas larger additions of up to 20 wt.% increase corrosion resistance and stability at high or low temperatures.
Overall, in comparison to carbon steels, alloy steels can exhibit increased strength, ductility and toughness. The disadvantages, however, are that alloy steels usually have lower machinability, weldability and formability.
Applications & examples
As the term alloy steel encompasses numerous types of steel, its application area is broad.
Low alloy steels are used in a wide range of industries due to their extreme strength, machinability, cost-effectiveness and availability. They are found in military vehicles, construction equipment, ships, pipelines, pressure vessels oil drilling platforms and in structural components. Examples include HY80 and HY100.
High-alloy steels can be expensive to manufacture and difficult to process. Nevertheless, their superior hardness, toughness and corrosion resistance make them ideal for structural components, automotive applications, chemical processing and power generating equipment. Examples of high-alloy steels include the grades HE, HF, HH, HI, HK, and HL.
Stainless steel
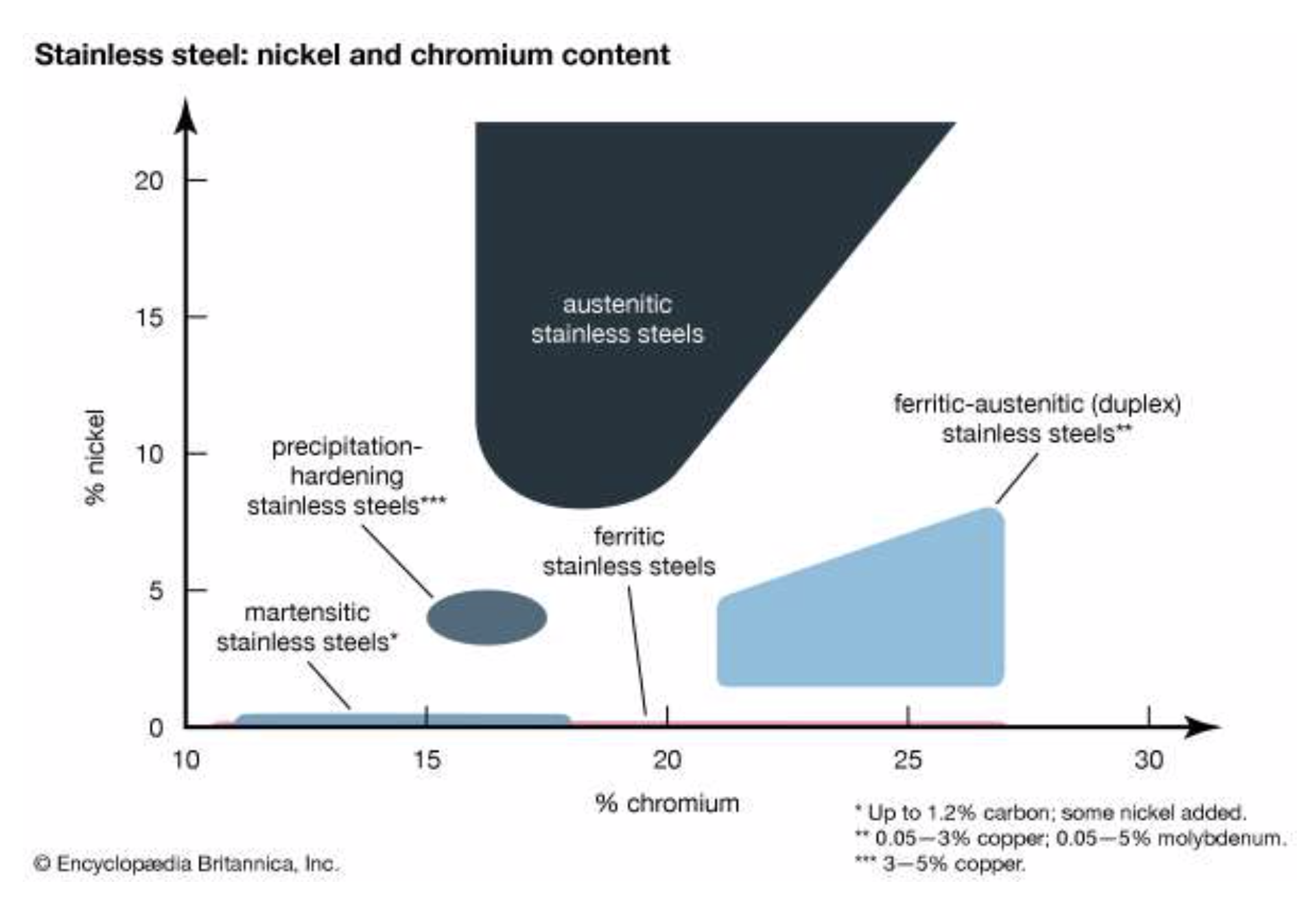
One of the most used steel in household items is stainless steel. Steel having 10% to 20% chromium makes steel stain free. There are three types of stainless steels namely austenitic, martensitic and Ferritic. Major applications of stainless steel are kitchen utensils, surgical items, dental equipment etc.
Stainless steel, any one of a family of alloy steels usually containing 10 to 30 percent chromium. In conjunction with low carbon content, chromium imparts remarkable resistance to corrosion and heat. Other elements, such as nickel, molybdenum, titanium, aluminum, niobium, copper, nitrogen, sulfur, phosphorus, or selenium, may be added to increase corrosion resistance to specific environments, enhance oxidation resistance, and impart special characteristics.
Most stainless steels are first melted in electric-arc or basic oxygen furnaces and subsequently refined in another steelmaking vessel, mainly to lower the carbon content. In the argon-oxygen decarburization process, a mixture of oxygen and argon gas is injected into the liquid steel. By varying the ratio of oxygen and argon, it is possible to remove carbon to controlled levels by oxidizing it to carbon monoxide without also oxidizing and losing expensive chromium. Thus, cheaper raw materials, such as high-carbon ferrochromium, may be used in the initial melting operation.
There are more than 100 grades ofstainless steel. The majority are classified into five major groups in the family of stainless steels: austenitic, ferritic, martensitic, duplex, and precipitation-hardening. Austenitic steels, which contain 16 to 26 percent chromium and up to 35 percent nickel, usually have the highest corrosion resistance. They are not hardenable by heat treatment and are nonmagnetic. The most common type is the 18/8, or 304, grade, which contains 18 percent chromium and 8 percent nickel. Typical applications include aircraft and the dairy and food-processing industries. Standard ferritic steels contain 10.5 to 27 percent chromium and are nickel-free; because of their low carbon content (less than 0.2 percent), they are not hardenable by heat treatment and have less critical anticorrosion applications, such as architectural and auto trim. Martensitic steels typically contain 11.5 to 18 percent chromium and up to 1.2 percent carbon with nickel sometimes added. They are hardenable by heat treatment, have modest corrosion resistance, and are employed in cutlery, surgical instruments, wrenches, and turbines. Duplex stainless steels are a combination of austenitic and ferritic stainless steels in equal amounts; they contain 21 to 27 percent chromium, 1.35 to 8 percent nickel, 0.05 to 3 percent copper, and 0.05 to 5 percent molybdenum. Duplex stainless steels are stronger and more resistant to corrosion than austenitic and ferritic stainless steels, which makes them useful in storage-tank construction, chemical processing, and containers for transporting chemicals. Precipitation-hardening stainless steel is characterized by its strength, which stems from the addition of aluminum, copper, and niobium to the alloy in amounts less than 0.5 percent of the alloy’s total mass. It is comparable to austenitic stainless steel with respect to its corrosion resistance, and it contains 15 to 17.5 percent chromium, 3 to 5 percent nickel, and 3 to 5 percent copper. Precipitation-hardening stainless steel is used in the construction of long shafts.
Tool steel
Tool steel contains tungsten, cobalt, molybdenum, vanadium as alloying elements. Tool steel applications include bars, sheets, strips, valve fittings, flanges, packaging items etc.
How steel is made from raw iron? And steel making Process.
- Steelmaking process involves removal of unwanted nitrogen, sulfur, phosphorus or any impurities from raw iron (pig iron having 4% carbon) and the addition of alloying elements like chromium, vanadium, nickel, cobalt etc.
- First raw material Iron ore, Limestone, dolomite, dunnite and coking coal is added to the blast furnace from the top.
- Lime, Dolomite is added to remove impurities during steel making process. It is used to remove the excess carbon, silicon, and manganese. While lime is used to remove the sulfur, potassium in addition to carbon, silicon, and manganese with dolomite.
- The raw material mixture is added from the top of blast furnace having the temperature of 200 °C from the top and 1600 °C at the bottom. The hot air is blasted at 1200 °C. The melted mixture is now pure iron having less than 2% carbon.
- Molten steel is poured for production of shaped castings and cast mold to produce ingots for forgings, billets, bars, sheets etc.
- Steel with fully relieved from oxygen is called fully killed steel.
- Hydrogen (H2) results in molten steel due to moisture which produces hairline cracks or flakes steel.
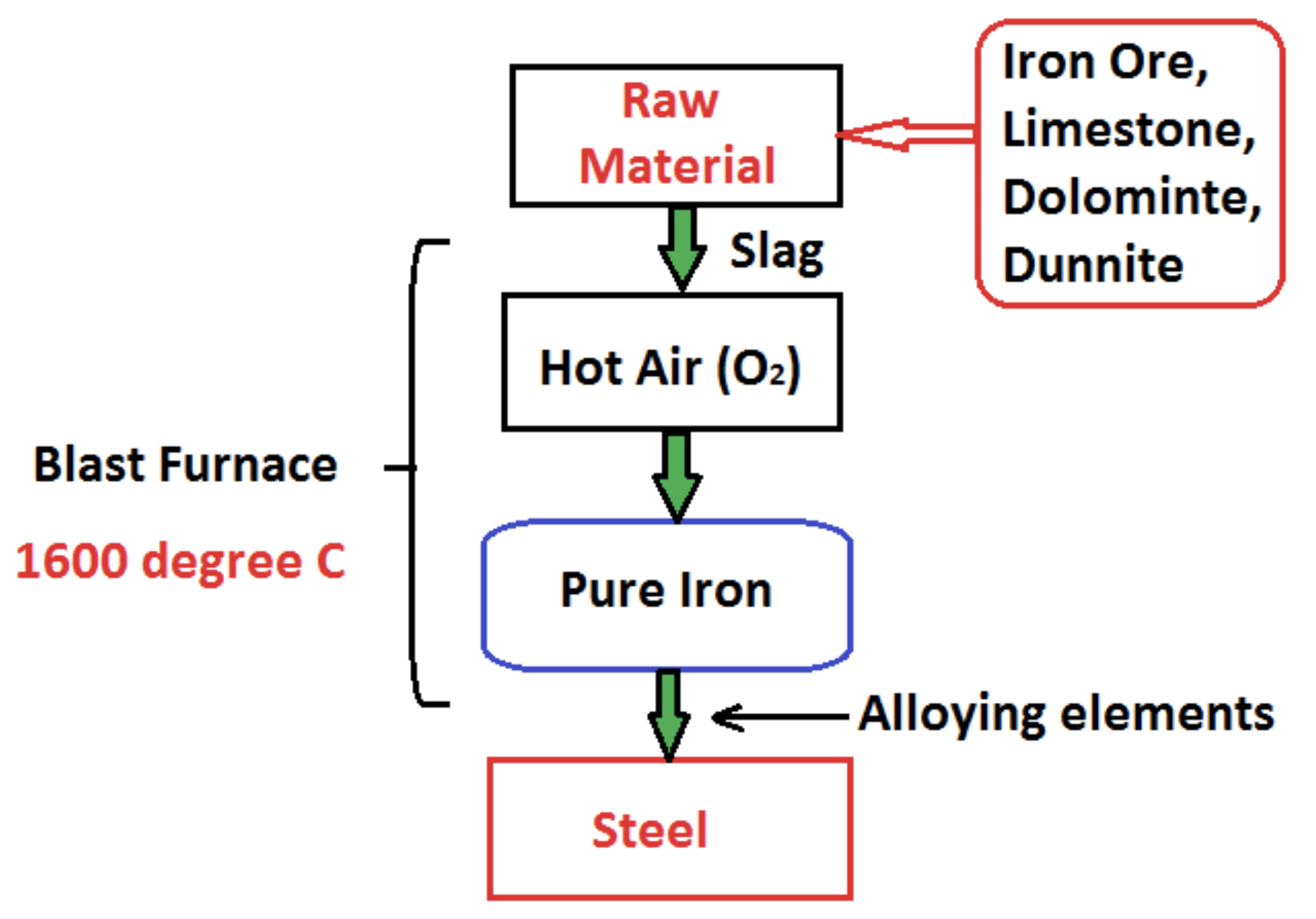
The steel is an alloy of iron with less than 2% of carbon. Various alloying elements are added to iron to get desirable properties. Steel is basically made up from iron ore (pig iron) and other raw materials which are heated in the blast furnace to give it a pure form.