What forms of corrosion will see in stainless steel
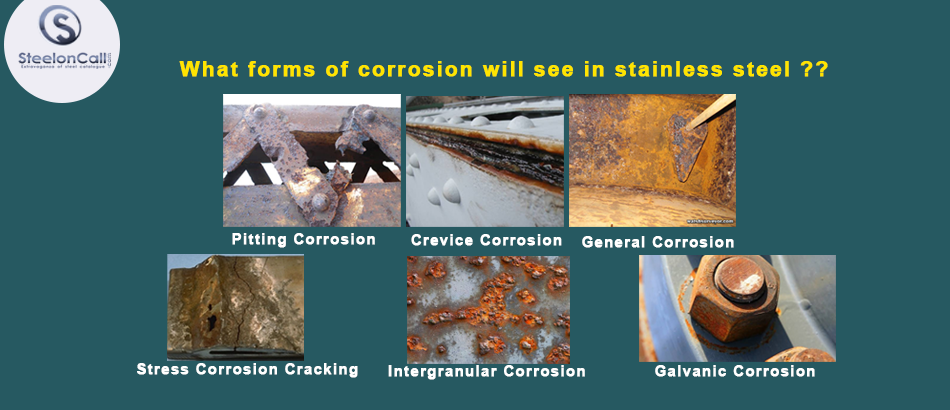
Stainless steels provide the most corrosion resistance because of their high amounts of chromium. This settles on grade 304, a magnificent decision when corrosion resistance is significant. Six types of corrosion are available on stainless steel. Steeloncall is going to clarify every corrosion type.
- Pitting Corrosion
- Crevice Corrosion
- General Corrosion
- Stress Corrosion Cracking
- Intergranular Corrosion
- Galvanic Corrosion
Pitting Corrosion: Certain synthetic species can attack the passive layer on stainless steel. The chloride particle Cl-is the most widely recognized of these and is found in everyday materials, for example, salt and blanch. Pitting corrosion is avoided by ensuring that stainless steel doesn't come into prolonged contact with harmful chemicals or by picking an iron evaluation, which is progressively resistant to attack. The pitting corrosion resistance can be evaluated utilizing the Pitting Resistance Equivalent Number determined from the alloy content.
Pitting resistance equivalent (PRE)
Evaluating the pitting resistance of stainless steel is through the pitting resistance equivalent (PRE), which can be determined from the steel's chemical composition.
PRE can be calculated easily with this formula:
% of Cr + 3.3 x % of Mo + 16 x % of N
Prevention of Pitting Corrosion:
Proper determination of materials with known protection from the service environment. Utilize higher alloys (ASTM G48) for expanded protection to pitting corrosion.
Crevice Corrosion: Crevice corrosion explains that the corrosion is happening in restricted spaces to which the working liquid's access from the earth is constrained. These spaces are generally called crevices. Examples of cracks are holes and contact regions between parts, creases, areas loaded up with stores, under gaskets or seals, inside breaks, and under slop heaps.
Prevention of Crevice Corrosion:
- Eliminate crevices in existing lap joints by continuous welding or patching.
- Avoid creating stagnant conditions and guarantee total waste in vessels.
- Utilize reliable, non-retentive gaskets, for example, Teflon.
General Corrosion- Stainless steel does not corrode as do ordinary carbon and alloy steels. In any case, with certain synthetic compounds, quite acids, the passive layer may be continuously attacked, relying upon concentration and temperature, and specific levels are especially forceful towards stainless steel.
- Facts in brief about uniform corrosion
- Uniform corrosion is the most notable corrosion type.
- Rates of uniform corrosion are communicated as a mass loss per unit area and unit of time.
Uniform corrosion on stainless steel happens for the most part with a presentation to solid acid or hot alkaline situations.
Stress Corrosion Cracking- A material failure might be quickened by the combined effect of corrosion and mechanical stress. Two instances of such forms are stress corrosion cracking and corrosion fatigue. Stress corrosion cracking (SCC) is the cracking induced by the consolidated impact of malleable and a negative situation. The effect of SCC on material, for the most part, falls between dry cracking and the fatigue threshold. The constant tensile stresses may be in the form of directly applied pressures or residual stresses.
Prevention Methods of Stress Corrosion Cracking
- Control of stress
- Control of environment
- Selection and control of material
- Testing of susceptible materials
Intergranular Corrosion: Intergranular Corrosion is generally called Intergranular Attack (IGA), which is a sort of corrosion where the limits of crystallites of the content are more vulnerable to corrosion than their internal parts.
Prevention Methods of Intergranular Corrosion
- Use low carbon (e.g., 304L, 316L) grade of stainless steel.
- Use post-weld heat treatment.
6. Galvanic Corrosion: When two unique metals or alloys are immersed in a destructive arrangement regularly associated with moisture, each will build up a corrosion potential. If galvanic corrosion conditions are available, the more respectable metal will turn into the cathode, and the more progressive metal will turn into the anode. A measurable amount of current will flow between the anode and the cathode. If this happens, the anode's corrosion rate in the administration environment will be increased. In contrast, the cathode's corrosion rate will decrease. The increased corrosion of anode is called galvanic corrosion. Principally, Galvanic corrosion (dissimilar-metal corrosion) is an electrochemical procedure wherein one metal corrodes, especially in electrical contact with another kind of metal, and the two metals are immersed in an electrolyte, for example, water.
Facts in brief about galvanic corrosion
- Issues with galvanic corrosion only from time to time happen between two stainless plates of steel
- Graphite gaskets should be avoided
- Galvanic corrosion occurs with two unique metallic materials in a corrosive environment.
- Examples of galvanic corrosion
- US Navy Littoral Combat Ship Independence
- Corroding lighting fixtures
- Lasagna cell
- Statue of Liberty
- Royal Navy and HMS Alarm
- Electrolytic cleaning.