What is D2 Tool Steel?
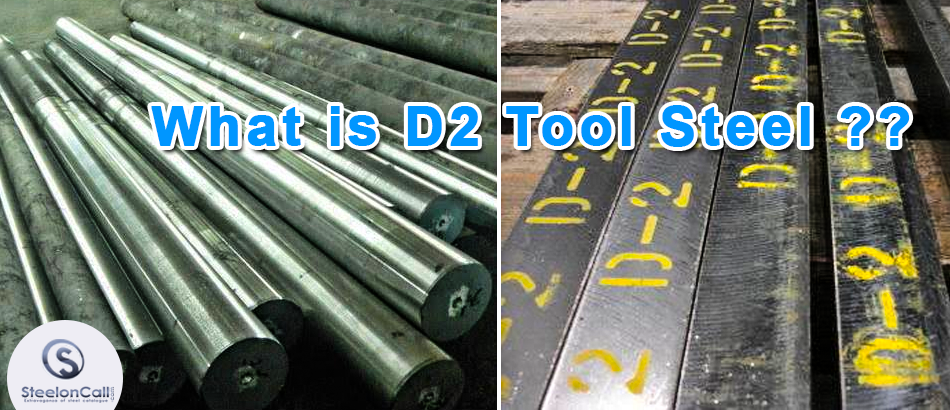
The D series of the cold-work class of tool steels, which initially included sorts D2, D3,D4,D5, D6, and D7 contains somewhere in the range of 10% and 13% chromium (which is strangely high). These steels hold their hardness up to a temperature of 425 °C (797 °F). Because of their high chromium content, certain D-type tool steels are regularly viewed as pure or semi-stainless, anyway their corrosion resistance is restricted because of the precipitation of most of their chromium and carbon constituents as carbides.
D2 tool steel is high carbon, high chromium tool steel and air-hardening very high wear resisting properties. It is an exceptionally hardening steel and will be practically free from size change after proper treatment. The high percentage level of chromium gives it mild corrosion-resisting properties in the solidified condition. It has low machinability and grindability, with a medium protection from decarburization. D2 is generally utilized in long creation, high wear applications, cold work applications and it is well known as a blade sharp edge steel. Some of the equivalent materials used in D2 tool steels are FED QQ-T-570, SAE J437, DIN 1.2379, NI KU, B.S. BD 2, ASTM A681, SAE J438 & UNS T30402.
Applications for D2 Tool Steel:
- Stamping or Forming Dies
- Forming Rolls
- Knives, slitters, shear blades
- Scrap choppers
- Tyre shredders
- Tools
- Punches
Characteristics of D2 Tool Steel:
- High carbon steel
- Extremely high wear resistance
- Low machinability
- Low grinding ability
- Virtually free from size change after treatment
- High percentage of chromium
Heat Treatment Process Involved In D2 Steel
Preheating: To limit distortion and stresses in enormous or complex tools use a double preheat. Heat at a rate not exceeding 400°F per hour (222°C per hour) to 1150-1250°F (621-677°C) equalize, then the heat will comes to 1400-1450°F (760-788°C). For typical tools, utilize only the subsequent temperature range as a single preheating treatment.
Stress Relieving: When desirable to relieve the strains of machining, heat D2 grade steel gradually slows to 1050°-1250°F, permit to equalize, and afterward cool in still air (Strain Relieving).
Forging: Heat gradually and consistently to 700°C then more rapidly to 900/1040°C. Try not to keep on manufacturing D2 below 925°C. Reheat as regularly as important to keep up proper forging temperature. After forging cool gradually. This isn't a strengthening procedure. After the forging process is cold, it must be annealed.
Quenching: D2 steel tool material is an air hardening steel and will create hardness on cooling in still air. To avoid scaling and avoid decarburization of the workpiece surface, controlled environment or vacuum heaters are suggested. If these furnaces are not accessible, pack solidifying, salt showers or enclosing the piece by tempered steel foil will give some level of surface security in the hardening process. Parts ought to be permitted to cool to 150F, or to where they can be held in the uncovered hand, and afterward temper right away.
Tempering: Heat consistently and altogether to the ideal temperature and hold for 25 minutes for every cm of thickness. D2 can be double tempering at around 15°C below the principal treating, after intermediate cooling to room temperature.
Annealing: Annealing must be performed after hot working and before re-solidifying. Heat at a rate not exceeding 400°F per hour (222°C per hour) to 1600-1650°F (871-899°C), and hold at temperature for 1 hour per inch (25.4mm) of greatest thickness. At that point cool gradually with the heater at a rate not exceeding 50°F per hour (28°C per hour) to 1000°F (538°C). Keep cooling to ambient temperature in the furnace or in air. The resultant hardness ought to be a limit of 255 HBW.
Relevant D2 Steel Specifications
Country |
USA, India |
German |
Japan |
Standard |
ASTM A681 |
DIN EN ISO 4957 |
JIS G4404 |
Grades |
D2 |
1.2379/X153CrMo12 |
SKD11 |
AISI Grade D2 Steel Mechanical Properties
Mechanical Properties |
Metric |
Imperial |
Hardness, Knoop (converted from Rockwell C hardness) |
769 |
769 |
Hardness, Rockwell C |
62 |
62 |
Hardness, Vickers |
748 |
748 |
Izod impact unnotched |
77.0 J |
56.8 ft-lb |
Poisson’s ratio |
0.27-0.30 |
0.27-0.30 |
Elastic modulus |
190-210 GPa |
27557-30457 ksi |
Thermal Properties Of D2 Tool Steel
Properties |
Conditions |
||
T (°C) |
Treatment |
||
Thermal expansion |
10.4 x 10-6/ºC |
20-100 |
– |
D2 Tool Steel Chemical Composition
ASTM A681 |
C |
Mn |
P |
S |
Si |
Cr |
V |
Mo |
||||||
D2 |
1.4 |
1.6 |
0.1 |
0.6 |
0.03 |
0.03 |
0.1 |
0.6 |
11 |
13 |
0.5 |
1.1 |
0.7 |
1.2 |
DIN ISO 4957 |
C |
Mn |
P |
S |
Si |
Cr |
V |
Mo |
||||||
1.2379/X153CrMo12 |
1.45 |
1.6 |
0.2 |
0.6 |
0.03 |
0.03 |
0.15 |
1.6 |
11 |
13 |
0.7 |
1 |
0.7 |
1 |
JIS G4404 |
C |
Mn |
P |
S |
Si |
Cr |
V |
Mo |
||||||
SKD11 |
1.4 |
1.6 |
0.6 |
0.03 |
0.03 |
0.4 |
11 |
13 |
0.2 |
0.5 |
0.8 |
1.2 |
*All the values that are expressed here by steeloncall are not exact values these are only for reference and approximate values only. Sprayform and powder metallurgy form have been delivered to improve the strength and refine the microstructure of D2. D2 has great wear resistance, hardness, andadequate strength.