Briefly Explain Deoxidation of steel
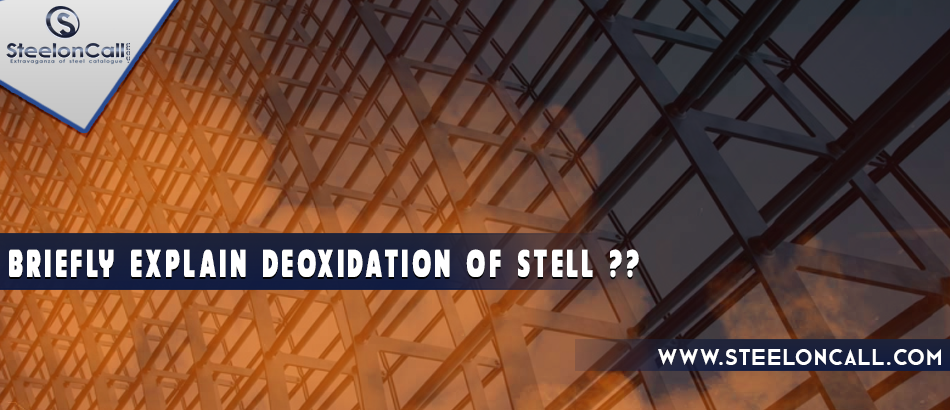
Deoxidation of steel is an innovative steelmaking activity, wherein the decreased concentration of oxygen dissolves in liquid steel to a necessary level. Deoxidized steel will be steel with a few or all the oxygen expelled from the softening during the steelmaking procedure. Liquid steels contain dissolved oxygen after their conversion from liquid iron. However, the solubility of oxygen in steel diminishes with cooling. As steel cools, excess oxygen can cause blow holes or accelerate FeO. Therefore, a few methodologies are there for deoxidation. It might be practiced by adding metallic deoxidizing operators to the soften either previously or after it is tapped. Even by vacuum treatment, in which carbon dissolved in the steel is the deoxidizer.
The deoxidation of liquid steel shows a paradox by increasing the concentration of deoxidizer. It dissolves over some basic value reoxidation of steel takes place. A couple of instances of the reoxidation of steel include the typical deoxidizers (Si and Al). Deoxidation is the last stage in steelmaking. In the Basic Oxygen Furnace and other steelmaking practices, the steel bath has the time of tapping and contains 400 to 800 ppm activity of oxygen. Deoxidation is possible during tapping. Include the tap-ladle appropriate measures of ferromanganese, ferrosilicon, or potentially aluminum or other deoxidizers. If the steel's carbon content is below specifications at the end of the blow, the metal is additionally recarburizer in the vessel. However, considerable increments in the scoop are unwanted due to the metal's unfavorable impact on the temperature.
THE FOLLOWING ARE THE FOUR TYPES OF DEOXIDATION OF STEEL.
They are ranging from wholly deoxidized to marginally deoxidized. They are like killed, semi-killed, rimmed, and capped.
KILLED STEEL DEOXIDATION:
Killed steel is deoxidized to such a degree, that there is no gas evolution during solidification. The use of aluminium in deoxidation is possible thanks to ferro-combinations of manganese and silicon. In some circumstances, calcium silicide or other unusual chemicals may be used solid deoxidizers is there. To limit piping, practically all killed steels are cast in hot-topped big-end up molds.
SEMI KILLED DEOXIDATION STEEL:
Semi-killed steel deoxidizes, not exactly killed steel. This outcomes within sight of only enough oxygen in the liquid steel to respond with carbon and structure adequate carbon monoxide to offset the hardening shrinkage. For the most part, this kind of steel has a carbon content inside the scope of 0.15–0.3% and finds full application in structural shapes.
RIMMED DEOXIDATION STEEL:
Tap Rimmed steels usually do not add deoxidizers to the iron in the heater or small increases to the liquid steel in the ladle. It is to guarantee adequate nearness of oxygen to encourage gas advancement by responding in shape with carbon. The specific methods followed rely on whether the steel has carbon content in the scopes of 0.12–0.15% or lower than 0.10%. When the metal in the ingot mold begins to solidify, there is an energetic advancement of carbon monoxide, bringing about an external ingot skin of generally clean metal low in carbon and different solutes. Such ingots are most appropriate for the production of steel sheets.
CAPPED DEOXIDATION STEEL:
Capped steel begins as rimmed steel; however, the part path through the solidification the capped ingot. It should be possible by actually covering the ingot shape or by including a deoxidizing specialist. The highest point of the ingot at that point structures into a secure layer of steel, yet the edge of the remainder of the ingot is more slender than in rimmed steel. Likewise, there is less isolation of polluting influences.
Deoxidation of steel by aluminum smothers the arrangement of carbon monoxide during solidification, which controls the formation of blowholes. There are many steel preparing tasks where aluminum executing of steel is undesirable. Steel is used for large castings are not killed with aluminum, because the suppression of carbon monoxide gas causes funneling defects, and also because the inclusion of alumina causes defective casting has been perceived from the beginning of continuous-casting operations that casting troubles and poor surface conditions are regularly experienced with aluminum-killed steels. As a result, several forms of steel deoxidation are preferred over aluminium slaughtered steel.The elective choices may incorporate silico-manganese deoxidation and, additionally, vacuum carbon deoxidation.