Can we use stainless steel as a coating material for mild steel?
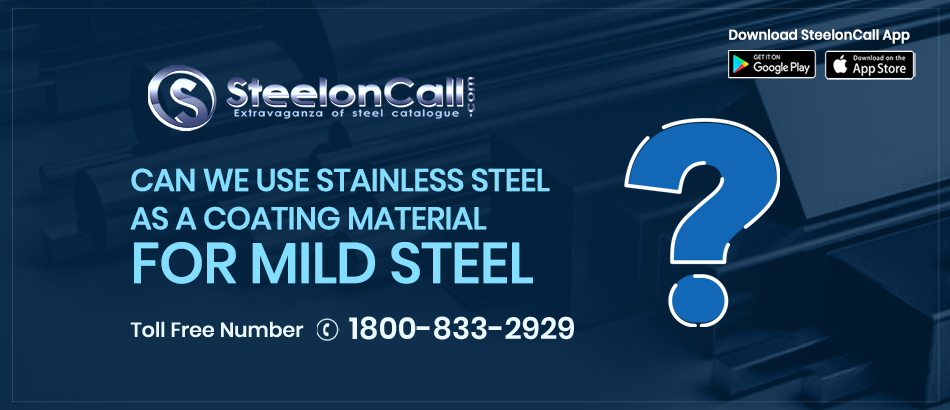
Mild steel may likewise be thought of as steel which isn't stainless. Mild steel and low carbon steels predominantly vary from stainless steels in having a much lower level of chromium. Stainless steels do contain a lot higher level of chromium than standard mild steels giving them superior protection from consumption yet at a higher budgetary expense. The high measure of carbon inside its structure makes mild steel helpless against rust. If one needs a rust-free sheet metal steel item, at that point surface completing will be required or stainless steel will need to be substituted for mild steel. One cannot coat stainless steel over mild steel in the customary sense. Be that as it may, fixing MS vessels or sheets with stainless steel sheets is broadly drilled, particularly in manufacturing stockpiling or reactor tanks. The essential tank structure is made with mild steel to give it the required strength. A thin sheet of the proper grade of stainless steel is welded to the MS sheet, to shape the contact surface of the vessel. This training is utilized to give the ideal concoction protection from the vessel.
Stainless steel is an alloy of nickel, iron and chromium. The melting point of chromium and nickel is a lot higher than iron which is the main element of mild steel. So to melt stainless steel one needs to dissolve chromium and nickel likewise and not just iron that is the reason treated steel has a higher softening point than mild steel. Stainless steels are gatherings of ferrous combinations that contain at least around 11 or 12% of chromium by mass and are basically made to have a level of protection from erosion or general rusting in mild atmospheric environments. The compound associations can lessen the pliability of ductility of stainless steel so it carries on increasingly like a fragile material when subject to pressure. Consumption under protection (CUI) is the most well-known reason for spills from process channeling or gear and is commonly the biggest upkeep cost for treatment facilities and compound plants, including significant personal time and making a critical hazard. Epoxy and epoxy phenolic coatings are used to reduce CUI, but they are more commonly used over carbon steel. Warm shower applied aluminium has been applied to the stainless steel used for extreme seaward, elevated temperature administration. The strategy for covering incorporates a sharp, exceptionally rakish surface profile and a film work of 200 to 250 microns of bend showered aluminum is applied, and afterward, a sealer layer of silicone aluminum is utilized.
Mild steel lacks the corrosion-resistant properties of its stainless steel counterpart. In spite of the fact that it's more grounded and more solid than stainless steel, carbon steel may rust and consume when presented to dampness. Indeed, even modest quantities of dampness, remembering dampness fume for the air, can cause carbon steel to rust. Moreover, mild steel is less bendable than stainless steel. With the metals normally utilized in designing, for example, carbon steel, treated steel, zinc, copper and aluminum, the common erosion procedure can be viewed as the thermodynamically preferred opposite response of the medal-winning process. Mild carbon steel was the material of decision for exhaust frameworks for a long time. An iron oxide covering on the fumes framework shielded it from environmental erosion to shifting degrees. Nonetheless, it experienced helpless consumption obstruction when presented to street salt and fumes condensate. Thus, exhaust frameworks produced using this material had a short life whenever presented to the earth experienced by numerous individuals on-street vehicles. Applications for carbon steel are presently constrained to choose nonroad applications that work in moderately non-destructive situations. The erosion obstruction of carbon steel can be extraordinarily improved using a hot plunged aluminum covering. This is regularly alluded to as aluminized steel. One especially significant ferrous combination alloying component is chromium. By including adequate chromium, stainless steel is formed. When stainless steel is heated, chromium shapes a defensive chromium oxide covering that postpones further oxidation. At least about 10.5% chromium is normally required to passivate the surface and to group material like hardened steel. Inasmuch as this oxide layer is steady and nonstop, the metal substrate is very much shielded from consumption. It ought to be noticed that nickel, while utilized in numerous grades of stainless steel, isn't contained in all grades of stainless steel.