Describe Desulphurization Of Steel?
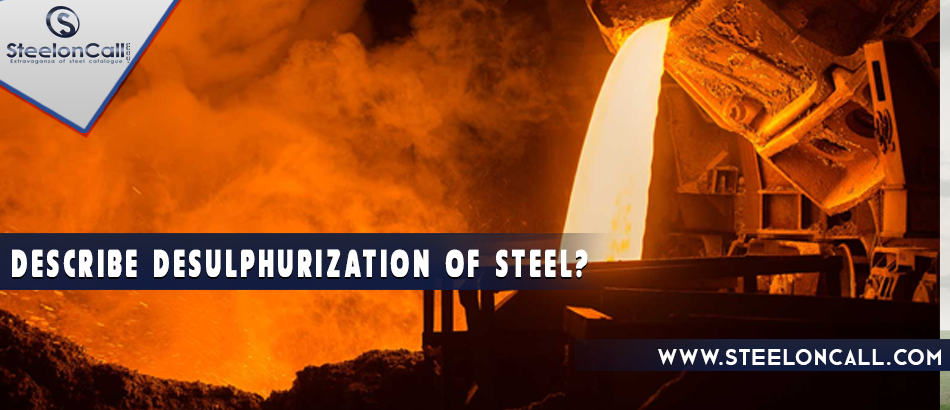
Desulphurization of steel during the secondary steelmaking process relies upon temperature, groupings of sulphur and oxygen in the steel, yet essentially on the synthetic arrangement and physical properties of slag. The refining of liquid steel during secondary steelmaking to meet the necessary compositional range requires the improvement of the procedure parameters. Steel is a significant material to fabricate the items in industries and life. It is made through numerous intricate procedures and much expense. Because of the worldwide challenge and clients needs, the manufacturers are presently constrained to improve the nature of the items, spare the expense and time for the desulphurization procedure for steel loss and temperature loss of the hot metal.
Sulphur is one of the most undesirable and inconvenient polluting influences inside the steel that unfortunately influences the properties and the nature of the steel. In this way, desulphurization (sulphur removal from liquid steel) is required as a key procedure that is chiefly accomplished in ladles during secondary steelmaking. In steel Desulphurization, several factors that simultaneously affect the extent of sulphur removal from the molten state is like steel-slag reaction, the oxidation state of the steel/slag, capacity/potential of the slag for sulphur removal, basicity/amount/viscosity and temperature and slag. One of the most critical enhancements in steel quality was the impediment of the sulphur content. That improvement was driven by the presentation of hot metal and steel desulfurization in incorporated steelmaking plants. A side effect was the possibility of enhancing the slag synthesis in the blast furnace with respect to increased efficiency and diminished expenses. Here, Steeloncall describes the state-of-the-art in desulfurization by clarifying the sources of sulphur in iron and steelmaking, the quality prerequisites of steel items and the desulphurization innovation.
DESULPHURIZATION OF STEEL BY SLAGS
The most popular strategy for desulfurization of steel is expulsion of sulphur from liquid steel to the essential diminishing slag. Essential slag is a slag containing for the most part fundamental oxides: CaO, MgO, MnO, FeO. A regular essential slag comprises 35-60% CaO + MgO, 10-25% FeO, 15-30% SiO2, 5-20% MnO. Progress of sulphur from steel to slag might be presented by the chemical equation:
[S] + (CaO) = (CaS) + [O]
The equilibrium constant KS1 of the reaction is: KS1 = a[O]*a(CaS)/a[S]*a(CaO)
Where
a(CaS) & a(CaO) - activities of CaS and CaO in the slag.
a[O] & a[S] - activities of oxygen and sulphur in the liquid steel
A similar response in ionic structure: [S] + (O2-) = (S2-) + [O]
The harmony consistent KS2 of the response is: KS2 = a[O]*a(S2-)/a[S]*a(O2-)
Where:
a(S2-) & a(O2-) - activities of S2- and O2- in the slag.
The capacity of slag to expel sulphur from steel is portrayed by the distribution coefficient of sulphur is
LS = (S)/[S]
Where:
(S) - grouping of sulphur in slag;
[S] - the grouping of sulphur in steel;
As shows up from the above conditions desulphurization is powerful in deoxidized (low (O)) essential (high (CaO)) slags. In this way, the capacity of the basic oxygen process (BOP) to expel sulphur is low because of its highly oxidized slag. Desulphurization might be viably directed in the diminishing slag phase of the steelmaking process in an Electric-arc furnace. At this stage, the oxidizing slag is removed and afterward lime flux is added to shape fundamental slag with high CaO content. Sulphur removal in the ironmaking and oxygen steelmaking process is checked on. A sulphur balance is made for the steel making procedure. There are four phases where sulphur can be expelled(removed) and they are described as, in the blast furnace, during hot metal pretreatment, in the converter and during the secondary metallurgy treatment.
For sulphur removal a low oxygen movement and an essential slag are required. In the blast furnace ordinarily, 90% of the sulphur is removed. Still, the hot metal contains about 0.03% of sulphur. Different hot metals desulphurization forms are utilized around the world. With co-infusion, sulphur concentrations below 0.001% are reached. Fundamental slag helps desulphurisation in the converter. In any case, sulphur increment isn't unprecedented in the converter because of high oxygen action and sulphur input through scrap and additions. For low sulphur concentrations secondary metallurgy desulphurization, with a decreased oxygen activity and essential slag, is constantly required.