What Are Different Types Of Tool Steel
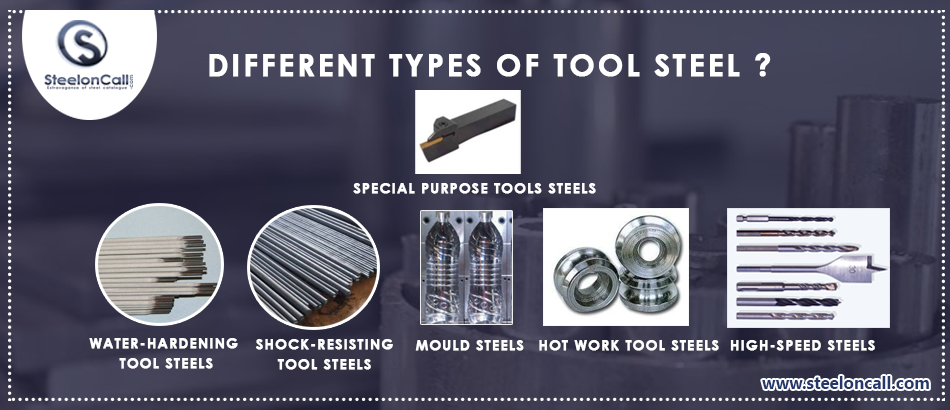
Tool steel refers to a variety of carbon and compound steels that are especially appropriate to be made into special building construction tools. Tool steels are utilized for cutting, squeezing, extruding, and coining of metals and different materials. Their utilization, for example, the creation of infusion molds, is essential, because of their protection to abrasion, which is a significant measure for a form that will be utilized to deliver a considerable number of moldings of an item or part. Their suitability originates from their unmistakable hardness and deformation and their capacity to hold a cutting edge at raised temperatures.
Therefore, tool steels are appropriate for their utilization in the forming of different materials. A few grades have extra protection to corrosion because of included synthetic properties, for example, vanadium. Likewise, with specific categories, the manganese content is limited to limiting the ability to break during water quenching.
Now, describes the classifications of toll steel in the below section.
- Water-Hardening Tool Steels (Symbol W)
- Shock-Resisting Tool Steels (Symbol S)
- Mould Steels (Symbol P)
- Hot Work Tool Steels (Symbol H)
- High-Speed Steels
- Special Purpose Tools Steels (Oil Hardening).
WATER HARDENING TOOL STEELS (SYMBOL W):
These Water-Hardening Tool Steels are plain carbon tool steels and are the most affordable. These steels have low special hardenability. W-group tool steel gets its name from its characterizing property of being water quenched. W-grade steel is high carbon plain-carbon steel. This gathering of hardware steel is the most regularly utilized tool steel because of its minimal cost compared to others. They function admirably for little parts and applications where high temperatures are not experienced; over 150 °C (302 °F), it starts to relax to a noticeable degree. Its hardenability is low, so W-group tool steels must be exposed to a fast extinguishing, requiring the utilization of water. These tool steels can achieve the high hardness and are relatively fragile contrasted with other tool steels.
SHOCK-RESISTING TOOL STEELS (SYMBOL S):
Shock-Resisting Tool Steels are the type of tool steel has been designed to resist shock at low or high temperatures. Its low carbon content is required to accomplish the essential sturdiness. This gathering of metals has high effect sturdiness, however a low abrasion resistance. Some typical applications of S-grade tool steel include Chisel Cold Working, Chisel Hot Working, Battering Tools, Boiler-Shop Tools, Chisel Blacksmiths, Chuck Jaws, Cold Gripper, Hot Gripper, Cold Swaging, Hot Swaging, Clutch Parts, Collets, Hot Trimming, Chipper Knives, Cold Shear and Hot Shear.
MOULD STEELS (SYMBOL P):
The Mould Steels need to withstand substantial weight (pressure) along with abrasive action of the molding powders. Accordingly, the outside of the molds ought to be challenging to face rough activity. The center of the patterns ought to be hard to withstand shock during the compression cycle. The outside of the mold should have a high finish to give excellent surface completion to the shaped items.
HOT WORK TOOL STEELS (SYMBOL H):
Hot Work Tool Steels are utilized to cut material at high temperatures. The H-Group has included quality and hardness for delayed presentation to raised temperatures. They are low in carbon and reasonably high in new composites. Some typical applications of H-Grade tool steel include Cores for Zinc and Aluminum, Hot Extrusion for Aluminum, Cold Heading Die Castings, Die Casting Dies, and Hot Forging.
HIGH-SPEED TOOL STEELS:
High-speed steels are exceptionally alloyed tool steels developed initially to do the high-speed metal cutting. First, high-speed steel was 18/4/1 (W/Cr/V)-Grade T1, which is yet to be utilized. Later, cobalt (5-10%) was added to the steels to increase hot wear resistance.
SPECIAL PURPOSE TOOLS STEELS (OIL HARDENING):
Oil hardening tool steels are broadly useful tool steel. They should be oil extinguished. Because of its resistance to abrasion and toughness, they are utilized for a broad scope of utilization. Applications include drill bushing, cold forming, thread cutting, collets, severe trimming, die blanking, gages, and knurling tools.
For assembling various tools devices that are useful for construction purposes with multiple properties that are valuable in the development structures and are required such as resistance to abrasion, hardness, and deformation and must have the ability to hold a cutting edge at high temperatures.