Hardening should never be the final heat treatment for steel why?
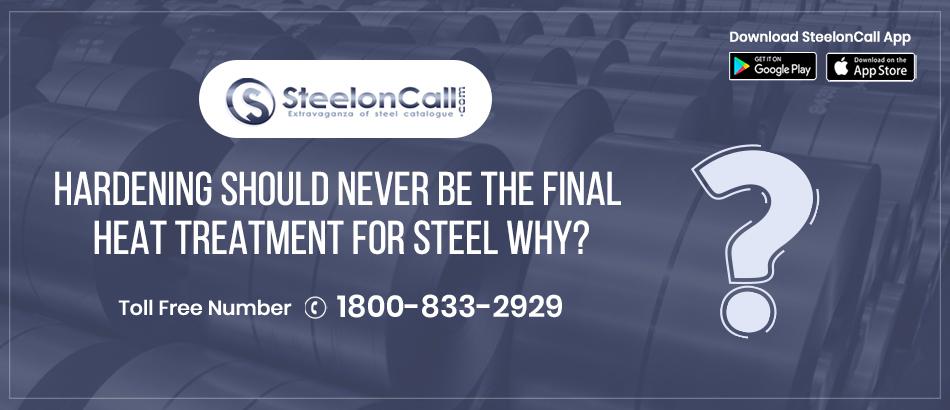
Steel parts frequently require a heat treatment to acquire improved mechanical properties, for example, expanding hardness or quality. The hardening cycle comprises heating the segments over the basic (normalizing) temperature, holding at this temperature for one hour for every inch of thickness cooling at a rate sufficiently quick to permit the material to change to a much harder, more grounded structure, and afterward treating. Steel is basically a combination of iron and carbon; other steel amalgams have other metal components in the arrangement. Heating the material over the basic temperature makes carbon and different components go into a strong arrangement. Quenching "freezes" the microstructure, instigating stresses. Thus, parts are tempered to change the microstructure, accomplish the suitable hardness, and dispose of the burdens. Hardening is the way toward heating the steel at a generally low temperature prompting precipitation and spheroidization of the carbides present in the microstructure. The Tempering temperature and times are commonly controlled to deliver the last properties expected of the steel. The outcome is a part of the proper mix of hardness, quality, and durability for the expected application. Tempering is likewise viable in easing the burdens instigated by quenching.
Beginning with blacksmithing, humankind has been working with steel for such a long time we've devoted whole enterprises to heating and molding steel mixes to meet our requirements. Today there are endless approaches to heat, twist, hardening and artificially modify the steel to fit whatever reason we need it to serve. During our vacuum heat medicines, steel is austenitized through a cycle of applying to shift high temperatures to the metal related to utilizing a halfway or hard compel vacuum to secure the material and abbreviate preparation time. This leaves the completed item less helpless to consumption, oxidation, and wear while improving quality and strength. While it is conceivable to harden steel inside a temperature scope of around 200 degrees and acquire what may appear to be acceptable outcomes, the best outcomes are obtained inside an exceptionally thin scope of temperatures near the decalescence point. The hardening temperature for both low tungsten and carbon steel can be situated with exactness, and the total change from delicate to hard happens inside a scope of 10 degrees F. or then again less. After the temperature has been expanded more than from 35 to 55 degrees F. over the hardening point, the hardness of steel is decreased by higher temperature, given the heating is adequately drawn out for the steel to be completely heated. It isn't remarkable for one to encounter issues after heat tempering metals. Even though it is one of the last stages during the assembling cycle, it is no less significant. When done appropriately, heat treatment can modify the mechanical and physical properties of metals without changing their shape. At the point when fouled up, the outcomes are not exactly alluring. It would be best if you guaranteed that the material is high-caliber by dodging steel heat treatment issues. Here is some data on normal heat treatment issues and how to maintain a strategic distance from them. For heat treatment, the steel is first heated to some temperature over the basic temperature to frame austenite. The pace of warming to the wanted temperature isn't significant. Notwithstanding, profoundly focused on materials created by cool work ought to be heated gradually than calm material to dodge twisting. In the wake of heating, the material is cooled at a rate that will bring about an ideal activity. Low combination metals and decarburization can cause overheating and consuming. Temperatures higher than 1200 °C pulverizes steel and other low composite metals. Some disintegration in mechanical properties can happen if the heat treatment is managed before manufacturing and other mechanical cycles. Mechanical lacks that happen from utilizing a lot of heat can influence the stainless metal's sturdiness and effect quality. A mechanical insufficiency can cause an orange stripe impact. The orange strip impact is when the surface has hard and weaknesses on top of it.
It might be conceivable to harden bigger segments in lower-grade preparations by utilizing non-standard medicines, such as quicker extinguish or lower-temperature tempers. Quicker extinguish rates consistently increment the danger of twisting or breaking, and low-temperature tempers can truly hinder mechanical properties, for example, sturdiness. Genuine thought ought to be given to these realities before requesting non-standard medicines to be done. Treated metal that requires a lot of heat influences the durability and quality of the metal. On the off chance that you notice that the outside of your metal has the sort of roughness you'd find on an orange stripe, with hard and weaknesses all over the place, it's been overheated. The effect of overheating isn't unavoidable. It's conceivable to dodge the effect by cautiously controlling the temperature of your heat source. By checking the instruments that you're utilizing, guaranteeing that they've been secured with hostile to decarburizing arrangements, guarantees that they're heated appropriately. Metal that is unevenly heated once in a while experiences being overheated fast. Permit it to gradually and normally chill off to stay away from these issues.