What Are The Best Metals For Welding Process And Their Applications
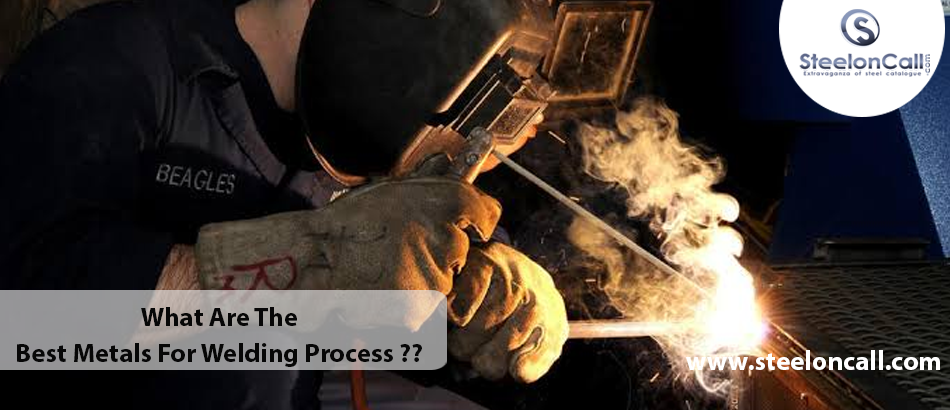
Welding is a process of combining at least two metal pieces by using heat and pressure. When heat is applied to metal, it turns out to be soft, empowering corridor to be joined by applying sufficient weight. Each metal and metal amalgamation reacts else to heat, and in the manner, they can be controlled.
Some of the significant advantages of the welding process on metals are that they're simpler to work (like a hot cement gun), can weld thinner accoutrements, use strong and flux-cored cables, and make it simpler to weld aluminum and Can be used with spool ordnance.
Welding is a complicated procedure that joins the study of electricity ( away from oxy- energy welding), heat, metallurgy, different countries of matter, and oxidation. This also implies multitudinous complications can crop, which can prompt weld failure. One way to reduce the threat is by choosing a metal that's effectively weldable and does not bear numerous redundantpre-weld andpost-weld operations to avoid weld failure. Some of the stylish metals for welding include
- Low Carbon Mild Steel
- Aluminum
- Stainless Steel
- Other Metals
LOW CARBON STEEL
Low carbon steel is weldable because it has further tensile properties than different types of steel. This is because it has deficient measures of carbon and follows rules of other alloying factors. This prevents the arrangement of brittle microstructures, for illustration, martensite. All of this eliminates the pitfalls of certain types of weld failures, similar as hydrogen cracking. As the measure of carbon supplements, so makes the trouble of making an respectable weld.
ALUMINUM
Creating a disfigurement-free weld in aluminum is different than welding steel, yet it should be possible by following the recommended rules. Picking the stylish possible is essential, as certain kinds are a lot simpler than others to weld. As a result of aluminum's high thermal conductivity, heat is moved down from the weld fleetly. Equipment with a advanced welding current might be needed to supply the necessary heat. As it cools, aluminum contracts altogether more than steel, so special care must be taken to help craters and to crack. Incipiently, the standard aluminum oxide covering the base metal can include pollutants and should be removed before welding to avoid porosity in the weld.
STAINLESS STEEL
Unlike plain steel, stainless is made to repel corrosion and is clean. This is fulfilled by adding 10 to 30 chromium to different factors, for example, iron. There's also a nickel compound available. Stainless is welded using bow welding (tig, mig, and stick). The debit is the more significant expenditure.
OTHER METAL TYPES
Some of the different metals, including magnesium, bobby, cast iron, titanium, and superalloys, similar as Inconel, can be welded. These will regularly bear extraordinary outfit and expert skill, making them less weldable for conventional job shops and specialists.
Welding processes have largely developed in recent times, offering rise to a variety of new and innovative strategies. Now one must have to understand these ways so that you know which bone is directly needed for your exertion. Each approach for welding has distinct advantages and disadvantages, and need to set aside the trouble to suppose about which procedure will be ideal for your operation.
APPLICATIONS OF THE STYLISH METAL WELDING PROCESS
MIG WELDING PROCESS
The Metal Inert Gas Welding – MIG is demonstrated when high inflexibility is admitted. The procedure consists in welding metals through the conformation of a wind of electricity ready to make a short circuit of power needed to weld together at least two shells. MIG welding both on slight or thick shells, beginning from your little housework till the most significant undertakings, for illustration, in the structure fields, auto, the development assiduity,etc.
TIG WELDING PROCESS
The Alternate type of significant welding operation is TIG Welding Method. This process is flexible and exceptionally performing; Tungsten Inert Gas welding-TIG has a series of advantages compared to the MIG Welding process, which allows one to get the most from the metal welding process. For case, TIG welding is preferred when a veritably high position of delicacy is needed. The TIG process has some specific features like largely concentrated and fluently controllable bow, Chronicity of emulsion, Good transfer of the padding material, and universal use.
These are the welding procedures with two most operations that are significantly employed for the development process. Also, the steel accoutrements that are directly welded for construction are available atsteeloncall.com.