What Is Corrosion Resistance Steel?
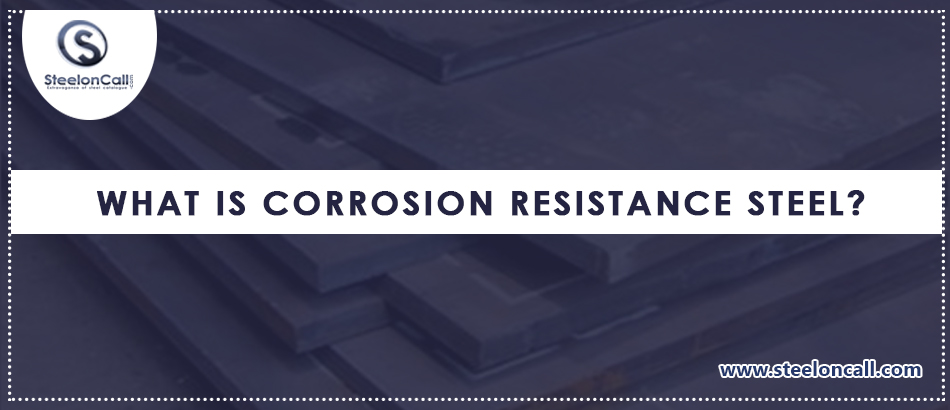
The best corrosion resistant steels in the world discover their way into countless applications, from protection to aerospace, turbines and many more. Steel that resists corrosion is often known as stainless steel or Inox steel. To make a metal less corrosive, it must be mixed with another metal and formed into a compound. Corrosion resistance or rustproof steel is a sort of steel, whose fundamental mentioned characteristic is resistance against corrosion (rust). It ́s alloy of iron, chromium and nickel who has content up to 30% of nickel or up to 2.5% of manganese or 10.5% – 30% of chromium. At the same time content absolutely amount of other austenite creative components, for example molybdenum, nitrogen, carbon, molybdenum and copper.
The approach they adopt is not typical of anyone else in the industry. All Metals & Forge has complete control over the construction, softness, and framing of all of their products. As the chromium content ascents in any stainless steel, so does its resistance to corrosion. Obviously, getting the best possible blend of ingredients is just a single little piece of manufacturing genuinely corrosion-resistant alloys. A great part of the rest has to do with different treatments, including heat treatment and surface conditioning. The corrosion resistant alloy that is generally applicable to countless industrial uses, from penetrating through aerospace applications.
Nowadays, corrosion-resistant metals come in any number of structures. One can get various moderations for heat, corrosion, strength and more, including broadly fluctuating hardness and weight. It is each of the matter of which metals that include what sort of treatments are utilized once the compound has been liquefied.
During the manufacture of stainless steel components or building structures it is possible to degrade the corrosion resistance. When austenitic stainless steels are exposed to temperatures ranging from 425 °C (797 °F) to 870 °C (1598 °F), this occurs. If the exposure time is excessively long, at that point the areas near the metal’s grain limits to lose their corrosion resistance and can be specially assaulted when presented to a corrosive environment then the grains dropout and the metal loses quality. This modification in microstructure has enhanced susceptibility to corrosion.
EXAMPLES OF STEEL CORROSION-RESISTANT ALLOYS:
Stainless Steel: Stainless steel types, for example, 304 or 316, are a blend of components, and most contain some measure of iron, which effectively oxidizes to shape rust. However, many stainless steel alloys also contain a significant amount of chromium (at least 18%), which is far more reactive than iron. The chromium oxidizes rapidly to shape a defensive layer of chromium oxide on the metal surface. This oxide layer resists corrosion, while simultaneously keeps oxygen from reaching the underlying steel. Different components in the alloy, such as nickel and molybdenum, add to its rust-resistance.
Copper Based Alloys:Other desirable properties consolidate with corrosion resistance to make copper-based alloys more attractive. Very great mechanical properties, thermal and electrical conductivity and ease of working with the material add to its utilization. While there are a few mixes and acids that forcefully attack these materials, they perform well in air, water, salt water, and in the presence of numerous natural and inorganic synthetic concoctions.
Nickel And Cobalt Alloys: 99.5% cast nickel grade is designed to resist hot burning arrangements and can be alloyed to increase strength. Nickel-copper Monel type alloys have generally excellent protection from chloride erosion. This grade can be provided with extra silicon and age solidified for increased strength where erosion-corrosion and bothering happen in chloride containing media. The nickel-molybdenum-chromium Hastelloy type grades give one of a kind of corrosion resistance to hydrofluoric, hydrochloric and phosphoric acid.
Iron and steel are the most usually utilized metals, corrode in numerous media including most outdoor atmospheres. Normally they are chosen not for their corrosion resistance yet for such properties as quality, simplicity of manufacture, and cost. These distinctions appear in the rate of metal lost because of rusting. All low-alloy steels and steels rust in moist atmospheres. In certain conditions, the expansion of 0.3% copper to carbon steel can reduce the rate of rusting by one quarter or even by one half. Corrosion resistance is the capacity to avoid natural deterioration by chemical or electro-chemical response. Alluring qualities of corrosion-resistant alloys, in this way, incorporate high protection to overall reactions inside the particular condition.