What is the Basic Oxygen Steelmaking Process?
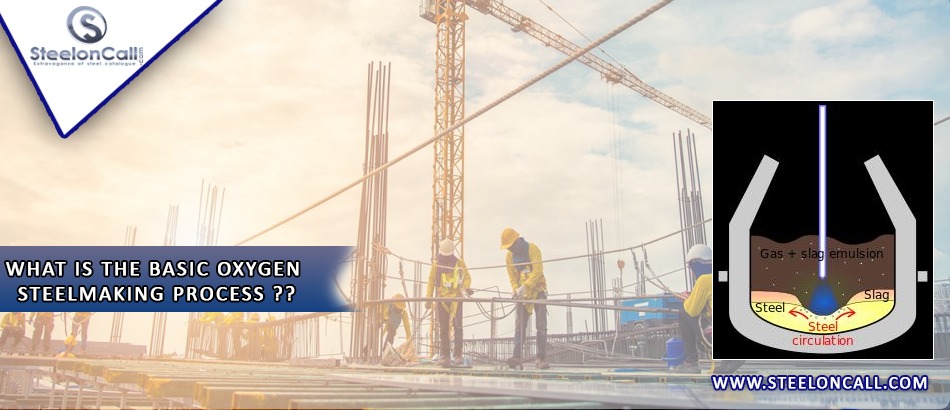
Steel is an ever- evolving material that has been the most preeminent of all materials since it can give a wide compass of parcels that can meet ever- evolving prerequisites. In this course, we explore both introductory and technical issues linked with brands, including iron and steelmaking, microstructure and phase change, and their properties and applications. Introductory Oxygen Steelmaking (BOS) is a primary steelmaking system in which the high- carbon molten pig iron is converted to steel. It's else called the Linz-Donawitz steelmaking process or the Oxygen Conversion process. The reason for the Basic Oxygen Steelmaking (BOS) process is to upgrade the hot metal delivered in the blast furnace into raw liquid steel, which might be latterly meliorated in the secondary steelmaking shop.
The introductory oxygen steelmaking is the point at which all the constituents are consolidated to make steel. The liquid iron comes through rail from the blast furnace in torpedo ladles. At the point when it lands at the BOS the torpedo spoon is sloped on its side and around 250 tons of liquid iron filled a hot metal pot. The introductory highlights of the BOS process are the partial oxidation of the phosphorus, carbon, silicon and manganese present in gormandizer iron and the going with a drop in the sulphur position.
BOS is a primary steelmaking process for changing over liquid gormandizer iron into steel by blowing oxygen through a shaft over the molten gormandizer iron inside the motor. The introductory oxygen steel- making process (BOS) is explained below by Steeloncall and as follows
- Liquid pig iron from a blast furnace iis filled with an enormous refractory-lined vessel called a ladle.
- The metal in the ladle is transferred directly for introductory oxygen steelmaking (BOS) or to a pretreatment stage. Pretreatment of the blast furnace hot metal is done ever to reduce sulphur, phosphorus and silicon before charging the hot metal into the motor. In outside desulphurizing pretreatment, a shaft is brought down into the liquid iron in the ladle and a many hundred kilograms of pulverized magnesium are included and the sulphur impurities are reduced to magnesium sulphide in rough exothermic response. The sulphide is also dredged off. Relative pretreatments are doable for outside desalinization and external dephosphorization exercising iron oxide and lime as fluxes. The choice to pretreat relies upon the nature of the hot metal and the necessary last nature of the steel.
- Filling the heater with the fixings is called charging. The BOS procedure is autogenous, for example, the necessary thermal energy is delivered during the oxidation procedure. Keeping up the stylish possible charge balance, the proportion of hot metal from fluxing to the cold piece is significant. The BOS vessel can be listed up to 360 ° and is listed towards the deslagging side for charging scrap and hot metal. The BOS vessel is charged with steel or iron scrap up to 25-30. Molten iron from the spoon is included as needed for the charge balance. Typical chemistry of hot metal charged into the BOS vessel is0.08 –0.18 P, 4 C,0.2 –0.8 Si and0.01 –0.04 S, which can all be oxidized by the handed oxygen away from sulphur which requires reducing conditions.
- The vessel is also set up and a water- cooled, copper sloped spear with 3 – 7 spouts are brought down into it and high chastity oxygen is conveyed at supersonic rates. The lance blows 99 pure oxygen over the hot metal, touching off the carbon broke up in the steel, to shape carbon monoxide and carbon dioxide, making the temperature lift to around 1700 °C. This melts the scrap, brings down the carbon substance of the liquid iron and helps to remove unwanted chemical elements.
- Fluxes are fed into the vessel to form a slag, to keep up basicity over 3 and retain contaminating influences during the steelmaking procedure. During blowing, agitating of metal and fluxes in the vessel frames an emulsion, that encourages the refining procedure. Near to the finish of the blowing cycle, which takes around 20 minutes, the temperature is estimated and tests are taken.
- The BOS vessel is listed towards the slagging side and the steel is poured through a valve hole into a steel ladle with introductory refractory filling and this procedure is called tapping the steel. The steel is also meliorated in the spoon furnace, by adding alloying accoutrements to grant extraordinary properties needed by the customer.
- After the steel is poured off from the BOS vessel, the slag is filled the slag pots through the BOS vessel mouth and ditched.
The main functions of the Introductory Oxygen Furnace Steelmaking (BOF’s) are to decarburized and expel phosphorus from the hot metal, and to upgrade the steel temperature so any farther treatments before throwing can be performed with insignificant reheating or cooling of the steel.