What Is the Difference between forged steel and cast steel?
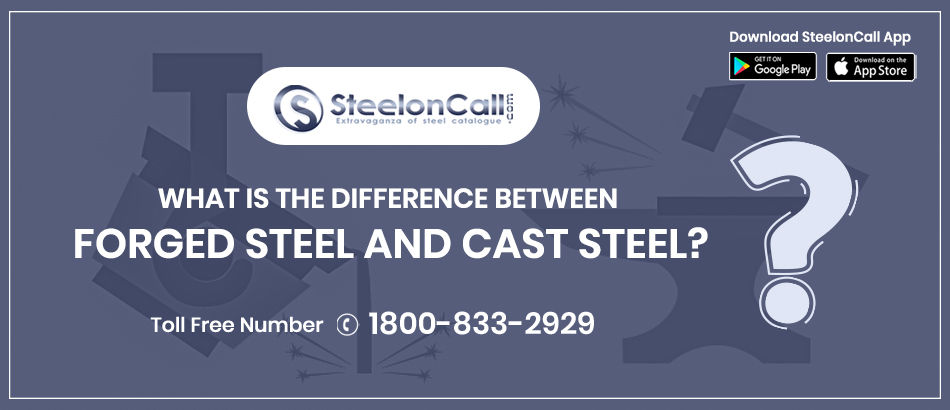
Casting is the process where metal is heated until liquid. While in the liquid or fluid state it is filled a form or vessel to make an ideal shape. Forging is the application of thermal and mechanical energy to steel billets or ingots to make the material change shape while in a strong state. Forged steel is commonly more grounded and more dependable than castings and plate steel because of the way that the grain streams of the steel are adjusted, adjusting to the state of the part. Both assembling measures require the use of high temperatures to steel crude materials and the execution of CNC machining work toward the finish of the cycle to get the eventual outcome. End results may likewise go through surface completion treatment, for example, painting, powder covering, cleaning, different kinds of covering (for instance zinc plating) and wear security/solidifying (utilization of tungsten carbide overlay). To wrap things up, cast and forged parts might be amassed, welded, brazed, hard-looked prior to being delivered as eventual outcomes.
Steel casting and forging are utilized to deliver parts for the accompanying industries:
- Water treatment
- Aeronautics
- Asphalt plants
- Stormwater parts
- Power generation and waste processing
- Mining and mineral processing
- Agriculture and livestock handling
- Rendering plants
- Automobile industry (pulleys and gear wheels)
- Materials handling
- Brickworks
- Railways
Forging and casting are two altogether different assembling measures used to control the state of the metal. In the casting process, metal is heated until liquid. At that point, it is filled with a form or vessel to make an ideal shape. In the forging cycle, the material is squeezed or pounded into a specific shape while still keeping up a strong state. Forged parts had a 26% higher elasticity than similar cast parts. Forged parts had a 37% higher weakness quality bringing about a longer life expectancy than cast parts. Cast iron just had 66% of the yield quality of forged steel, an estimation that demonstrates the heap sum metal can hold prior to distorting. The forged parts had a 58% decrease in the territory when pulled to disappointment, contrasted with a 6% decrease for cast parts. That implies steel forged parts consider a lot more prominent twisting before disappointment than cast parts. Forged and Casting are two altogether different assembling techniques. When something is cast, the material is heated over its softening temperature and filled with a shape where it sets. When something is forged it is actually constrained into shape while staying in a strong state, despite the fact that it is regularly heated.
STEEL CASTING BENEFITS
- Melting of metal permits it to be framed into a more prominent assortment of shapes, which considers more noteworthy adaptability to a limited extent plan
- Beginning outcomes are frequently nearer to plan details, decreasing time spent on optional machining and preparing
- Cast parts are almost consistently lighter than their forging counterparts
- Changes of part plans and related molds are relatively simple and speedy to executives.
- The strategy for modifying the metal's grain structure regularly prompts prevalent basic trustworthiness and mechanical quality
- The cycle of forging is commonly more affordable than casting gratitude to less escalated work prerequisites and less association of material piece
- Forging, all things considered, take out surface porosity alongside voids and different deformities
- Forging Is more predictable in the yield of created parts and in delivering parts that are fantastically solid and pliable
STEEL FORGING BENEFITS
The main difference between steel casting and steel forging is that the forging is precisely worked after hardening. This mechanical working bestows directionality, or anisotropy, to the forging. Castings and forgings are both helpless to assembling issues and misapplication by the purchaser. All in all, a forging is most appropriate to straightforward setups that can be handily worked in a kick the bucket or other tooling. It is additionally fit to applications in which the chief applied anxieties are equivalent to the bearing of mechanical working. Casting is most appropriate to complex shapes, custom or customized sciences, and to applications that are liable to multi-hub stresses. The primary distinction between casting and forging is that the last part shape is made when the liquid metal sets in the form. Since the sand form delivers the ideal completed shape, all that remains is to deal with the casting through different completing tasks in the foundry. This preparation doesn't change the directionality of the casting. A steel casting is homogenous. This implies that the mechanical properties of casting are similar, paying little heed to the course of applied anxieties. Cast iron can't be welded dependably because of its high carbon content, which would cause a fragile weld. Thus, this material doesn't give the quality and pipeline networks that are basic for high-weight and high-temperature applications. In these cases, casted steel is the most ideal choice.