What Is the Heat Treatment Process Of Steel Casting?
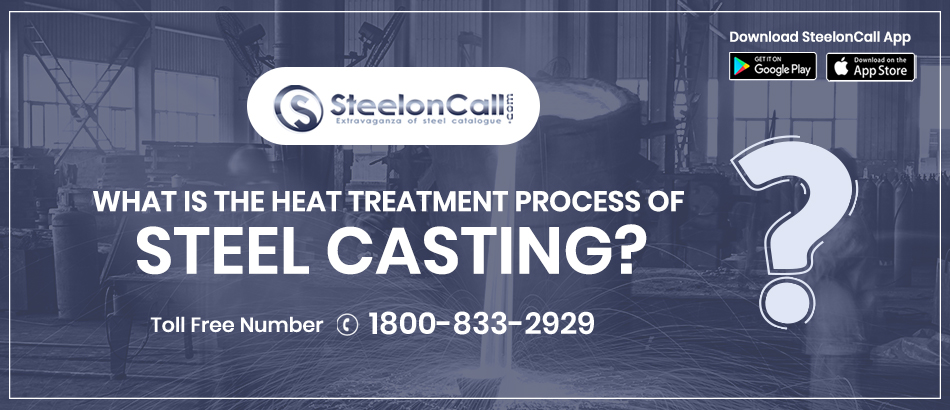
Carbon and low alloy steel castings are utilized in parts for railroad vehicles, siphons and valves, substantial trucks, development and mining gear, and force age hardware. Great applications use the exhibition of steel with the adaptable calculation of a casting. Steel castings offer high mechanical properties over a wide scope of working temperatures. The substance piece and microstructure of a steel casting decide its mechanical properties. Heat treatment can alter the microstructure of a material and give it a variety of mechanical qualities. A specific area's reaction to heat treatment becomes toughened. Steel with a high hardenability will have a more consistent hardness across thicker segments than steel with a low hardenability. Heat treatment of castings is principally used to adjust the physical, and now and again compound, properties of the cast composite. Huge numbers of the mechanical properties of both ferrous and non-ferrous combinations are controlled by their microstructure. Heat treatment Is an effective method of controlling the translucent structure of the combination to alter its mechanical conduct in an anticipated manner. Controlled heating and cooling can affect properties, for example, hardness, quality, sturdiness, malleability and versatility albeit changing the properties of one to accomplish an ideal result will regularly change another not generally an attractive way.
The Heat Treatment process of Steel Casting happens in 03 stages and they are like
- heating for quenching
- quenching
- drawing
HEATING FOR QUENCHING
Heating for quenching is best directed gradually, particularly on account of castings of variable thickness. Breaks may happen either in heating or in cooling, because of various temperatures at various purposes of the casting. The castings ought to be completely splashed at the greatest temperature (for the most part 1,500° to 1,600° F.), 1 hr. being adequate for segments 1 ft. in thickness. The base temperature that will provide the best solidifying effect will be discovered to be the most palatable in all situations, since the grain coarsens when the fundamental reach is exceeded to an extreme degree. All temperatures should be administered by a checked pyrometer with the hot intersection to the heated item, and with a few couples in a huge heater to guarantee a uniform temperature.
QUENCHING PROCESS
The casting should be moved as fast as conceivable from the heater to the quenching shower, and on account of enormous castings, for example, train outlines, this is in no way, shape or form a basic issue. The bigger castings are best dealt with by methods for cranes and rollers. The quenching operator utilized is by and large water or oil, ideally the previous, on account of its affordability and exceptional cooling impact, all the more promptly separating the coarse cast-steel grain. With unpredictable castings, it is commonly best to utilize oil. With water, it is conceivable to have an enormous tank and a huge running stream, serving to keep up a uniform temperature. Castings ought to never be tossed and to lay on the lower part of the tank, however ought to be unsettled to forestall the arrangement of a covering of fume, impeding the quenching impact. It is likewise best, at whatever point conceivable, to quench the thicker segments first.
DRAWING OPERATION
Normalized steels are more grounded and harder than annealed steels. In the standardized condition, steel is a lot sturdier than in some other auxiliary condition. Parts exposed to affect and those, which require the greatest sturdiness with protection from outside pressure are by and large standardized. In normalizing, the mass of metal affects the pace of cooling and the subsequent structure. Dainty pieces cool quicker and are sturdier subsequent to normalizing than thick ones. At whatever point conceivable, the drawing ought to be done in a shower or something to that effect, for example, lead, barium chloride, a barium chloride-salt blend, or oil. On account of enormous castings, this is obviously inconceivable, and incredible consideration ought to be practiced in getting a uniform temperature in the drawing heater.
The structure of cast steel casting conditions requires changes that apply to essentially a wide range of cast steel grades. Because of heating and cooling, Useful changes in mechanical and furthermore different properties for example hardness, erosion opposition and wear obstruction are obtained. This section incorporates the sorts of heat treatment of cast steel, conceivable down to earth impacts after every treatment and the basic changes caused during its course. There are instances of the microstructure in steel casting conditions, subsequent to quenching and in the wake of hardening at different temperatures.