What Is The Manufacturing process of TMT Bars
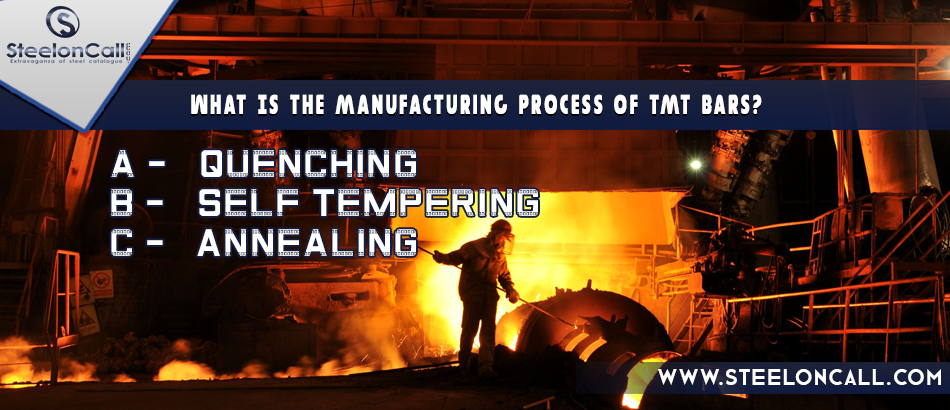
We all know that TMT is essential for a wide range of development purposes, yet it is additionally imperative to know what is the manufacturing process of making TMT bars. Best Quality TMT Bars go through a progression of procedures that decides the quality and adaptability of it. The manufacturing process of TMT Bar involves a series of procedures including rolling, water quenching, heat treatment, cooling at different phases of manufacturing. TMT bars are commonly hot-rolled from steel billets and are exposed to a programmable logic controller for the thermo-mechanical treatment. TMT steel rebars are the most utilized steel strengthened bar in the construction field. These bars are known for their substantial tensile strength and flexibility. There are different grades for TMT rebars to be specific Fe 415, Fe 500, Fe 550, Fe 600. Before TMT rebars, other steel rebars, such as Mild steel and HYSD steels, were used as reinforcements to concrete. Yet, these steel rebars didn't have adequate rigidity to help higher heap of structures; thus, TMT steel rebars were presented. The manufacturing process of TMT steel rebar as other steel bars however, what recognizes TMT steel rebar is the new advances engaged with it's making. The manufacturing process of TMT Bars involves the three different kinds of steps, and they are like
- Quenching
- Self Tempering
- Annealing
QUENCHING:
Quenching is the primary and first critical step in the manufacturing process. In the initial phase, Once the hot-rolled bars discharge from the completed factory, it enters the water splash framework known as the Thermax system. The best quality TMT bars fabricating process utilizes Thermax technology that cool down the external center quickly and guarantees the malleability of TMT rebars. Fast cooling solidifies the TMT rebars' outer center to a profundity improved for each area. It shapes a martensitic edge while the core remains hot & austenitic. This cooling innovation is known as the quenching process of TMT Bars.
SELF TEMPERING:
The second stage in the TMT manufacturing process is self tempering. In this stage, the residual heat moves from the center to the external layer, further hardening the martensite layer i.e., makes the bar harder. Since this procedure finishes by the heat left in the core, this stage got its name. Once the rebars are out of the thermex quenching box, the center stays hot contrasted with the surface permitting heat to spill out of the center to the surface, causing tempering of the external Martensite layer, framing a structure called tempered martensite.
ANNEALING:
The final stage in the TMT rebar manufacturing process is the annealing stage. In this annealing stage, the bars are presently at uniform temperature are then left to cool generally despite everything air to encompassing temperature. At this stage, the residual austenite changes to a refined, extreme, and ductile ferrite and pearlite core, which decides the flexibility of the bars.
Every one of these stages accomplishes without the addition of costly alloying components, which makes the TMT steel economically effective to deliver joined with the right balance of strength and flexibility ratio, this makes TMT bars the most favored bars for support. While picking the fortified bars consistently makes a point to lean toward the correct grades as the TMT steel bars are ordered by various categories, which are based on their tensile strength. Under thermomechanical treatment, the steel bars are gone through an exceptionally planned water-cooling framework where they are kept till the bars' external surface gets colder while the core remains hot. This makes a temperature inclination in the bars. After the escalated cooling, the bar is presented to air, and the center re-heats the quenched surface layer by conduction, therefore tempering treating the outer martensite. When the bars are removed from the cooling framework, the heat streams from the core to the outer surface, further softening the bars, which encourages them to achieve a better return quality. The subsequent heat-treated structure gives better quality and strength than the bars.