What is welding carbon steel?
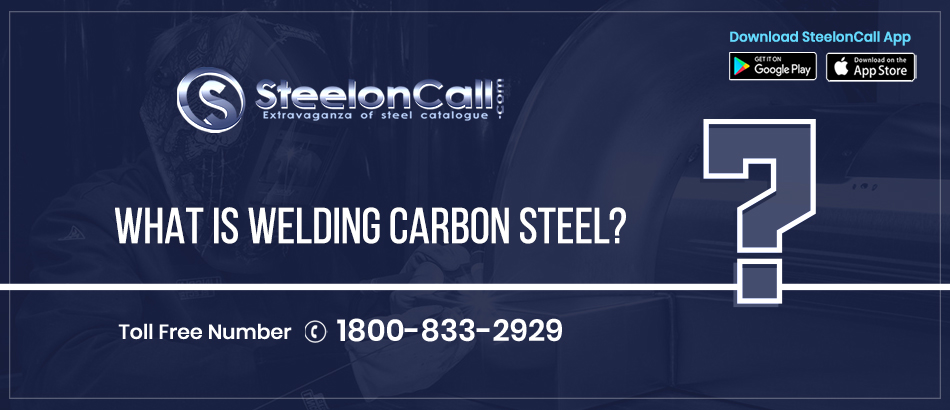
Low-carbon mild steel is not only the most often used metal, but it is also the easiest to weld. Despite the fact that most steel welding nowadays is done using covered anodes or one of the consumable-wire circular segment welding forms, oxy-acetylene welding of steel is still widely used, especially in thicknesses of 1/4 in. (6 mm) or less. An all-around prepared oxy-acetylene welder, chipping away at steel 1/8 in. (3 mm) thick, can, as a rule, make welds of excellent quality over the standard curve welder and make them nearly as quickly. As a rule, splits in medium/high carbon steel can happen when some time has slipped by after welding wrapped up. These breaks are called cold splits or postponed splits. Even though cementing interruptions that can occur following welding completed are not uncommon, the postponed splits occur more frequently. Welding steel is truly major to figuring out how to weld. Steel is mostly iron and carbon with modest quantities of other stuff like manganese. Low carbon steel has .3 percent carbon. Not 3 percent but rather 0.3 percent or point 3 percent. That is very little. For correlation purposes, cast iron has an entire 3 percent and now and again more. That is the reason solid metal is such a torment to weld. Furthermore, low carbon steel is the most straightforward metal to weld; low carbon steel is also the least expensive metal to purchase.
Welding carbon steel is pure and doesn't have any real obstacles. It welds fine in all positions and creates a quality weld. The main conceivable issue could be from welding in the vertical up position. This position typically requires a depression because the weld is, in every case, extremely curved. Another aspect to keep an eye out for is a cold lap. Mig welding can create low-quality welds if the welder isn't run hot enough. Other than that, it is an excellent decision for welding in a shop since it makes superior welds that are perfect and require next to no dressing. Scatter can be an issue now and again; however, that is explained against splash showers or only light scratching in the wake of welding.
All in all, no troubles are experienced when low welding carbon prepares. Appropriately made little carbon steel welds will approach or surpass the base metal in quality. Low carbon develops delicate, malleable, rolled, punched, sheared, and worked when either hot or cold. They can be machined and are promptly welded. Cast steel has a harsh, dull dark surface aside from where manufactured. Moved steel has fine surface lines running one way. Fashioned iron usually is conspicuous by its shape, hammer checks, or balances. The break shading is brilliant glasslike dim, and the flash test yields flash with long, yellow-orange streaks that tend to blast into white, forked sparklers. Steel emits sparkles when dissolved and cements in a split second. Low carbon can be handily welded with any circular segment, gas, and obstruction welding forms.
When welding is finished, permit segments to cool to 180°c before treating. Temper for 2 hours. Cool to 200°c at a controlled cooling pace of 100°c/hr highest. Cool to room temperature in still air. It might be essential to think about middle, lower temperature stress alleviation treatment in minimal conditions. To hold the segment at a center of the road temperature after welding, pending warming for treating, the accompanying elective techniques (underneath) could be applied. If the restriction is exceptionally high, this electoral method may not forestall the event of hydrogen initiated breaking.
The weldability of carbon steel is controlled via carbon proportionate (ce) for anticipating/evaluating preheat temperatures necessary for weld uprightness of the weldment. A first job in the mechanical properties of the weldment, hence, meticulously choosing welding procedure and boundaries to hinder the cooling rate are guaranteed by sound weld quality and break free weld (improved assistance execution). This exploration work surveys the impacts of different welding procedures and boundaries on microstructure and mechanical properties of carbon prepared in circular segment based welding. Welding limit of medium and high carbon preparedness is low, and this causes splits toward the finish of the welding pool or in the delicate heat zones. If this circumstance occurs, it expects welders to preheat and nearby heat the regions of welds. If neighborhood heat happens around the welding site, the temperature is at 650 - 700 degrees celsius.