Who developed a new way to make steel?
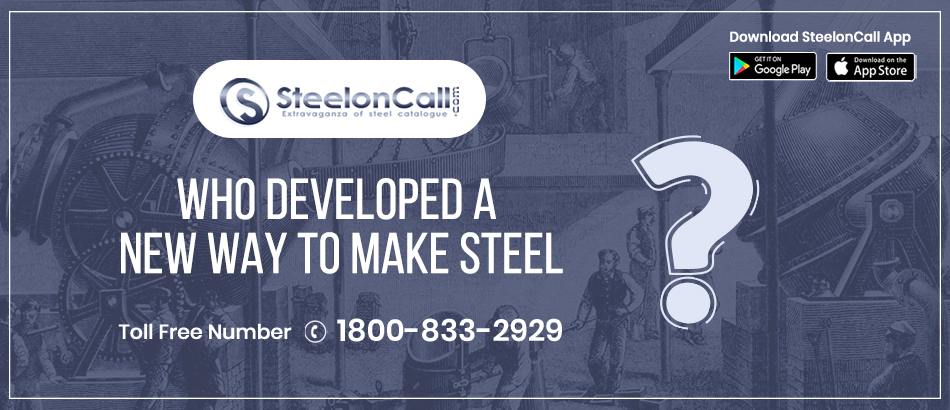
Iron is fairly simple to decrease over 800°C. One can make an expected iron metal blended in with charcoal pieces, form a mass of dirt around it, set its land through a gap in the base, and blow air with roars for a few hours. At that point, let it cool for a day or two, break the dirt and discover a blend of iron and minerals. This was brought in German by Lupe''. You eliminate the majority of the minerals, and you take the luppe to the fashion. You hammer it super hot on the iron block; the iron is anything but difficult to distort while the rest of the minerals are not delicate at this temperature, so you oust them like orange pips. Holding it some time in the focal point of the manufacturing fire where there is less air, it retains some carbon and transforms into steel. I don't imply that it's simple, yet it was done thusly for in any event 2500 years. As the steel may contain crushed minerals that would give a frail point, it was given in strips. To make a blade, the strips would be produced together, one next to the other. It was artistry over a science. The cutting edge measure is named after its designer, the Englishman Henry Bessemer, who took out a patent on the cycle in 1856. The cycle was supposed to be autonomously found in 1851 by the American creator William Kelly; however, the case is disputable. The cycle utilizing a fundamental stubborn coating is known as the "essential Bessemer cycle" or Gilchrist, Thomas measure after the English pioneers Percy Gilchrist and Sidney Gilchrist Thomas.
On a day lost to history, some serendipitous people found a flickering shooting star, generally iron and nickel, that had surged through the environment and collided with the ground. Consequently started a fixation that grasped the species. Throughout the long term, our progenitors would work the material, finding better approaches to draw iron from the Earth itself and, in the end, to smelt it into steel. We'd battle about it, make and annihilate countries with it, develop worldwide economies by it, and use it to construct the absolute most prominent innovations and structures the world has ever known. The Bessemer cycle was the principal modest modern cycle for the large scale manufacturing of steel from liquid pig iron before advancing the open hearth heater. The key guideline is the expulsion of contaminations from the iron by oxidation with air being blown through the liquid iron. The oxidation likewise raises the temperature of the iron mass and keeps it liquid.
A group of specialists from a few organizations in China and Taiwan has built up another approach to make steel that offers more quality and flexibility. The specialists built up another method they call distorted and divided; they can't give all the subtleties, obviously, because that would keep them from gaining by what they have made. However, they do unveil that it has a place with a class of metal that the business has characterized as "advancement prepares," which are medium manganese preparations made with Carbon is 0.47 percent, manganese is 10%, vanadium is 0.7 percent, and aluminium is 2.0 percent. The report likewise that the cycle includes cold moving, which is followed up by hardening in a low-temperature condition, and that metastable austenite grains are installed someplace simultaneously, they note, holds flexibility while taking into consideration controlled deformities that invigorate the metal. The gathering claims that the outcome is asteel with a yielding quality of 2.2 GPa and 16 percent uniform stretching, which would make it the best in its group. They propose the ideal properties are because of the kind of lattice framed during the rolling and treating measure.
In different structures, the blast furnace has remained the workhorse of overall virgin iron creation for over 200 years, delivering carbon-soaked "hot metal" for ensuing preparation by steelmaking measures. Nonetheless, the cutting edge impact heater has progressed far from its previous precursors. Most present-day enormous limit impact heaters speak to very productive concoction reactors, equipped for stable activity with a noteworthy scope of reactant feed materials. The infusion of pummeled coal, flammable gas, oil, and, sometimes, reused plastics to supplant a segment of the metallurgical coke utilized as the essential reductant and wellspring of concoction All the meantime, vigour indicates a big improvement.